
All posts and comments are to be civil.Where you can find DIY, FAQ, and more! Subreddit Rules And really glad I didn't destroy my barrel doing this.Welcome to /r/AR15! Here for your favorite black gun links, build photos, questions and other tactical or practical info.
Best ar 15 muzzle brake 2016 install#
It was a PITA but I feel pretty good that it's attached securely and its not going to come off when I install and take off my Recce 5 can. If I couldn't use a good barrel clamp, it would have been a futile exercise. You have to use a good anti-seize grease, tighten and loosen several times, and play with the shims, but I was able to get the brake timed with 460 in-lbs (wrench will go to 600 in-lbs). 35 ft-lbs while trying to time the brake is a big pain in the butt. Amazingly enough, this made the wrench fit snugly. The crow's foot wrench is a bit loose on the taper mount flats but I put a layer of painters tape on flats. Fortunately, I have an old 3/8" inch drive Craftsman torque wrench (back when they were made in the US and have a lifetime warranty). The only ones I could find are for a 3/8" drive. I struggled with this and decide to buy a 3/4" crow's foot wrench. They provide shims with their taper mount brakes so that you can time them properly. Griffin Armament recommends that their taper mounts get torqued to 35 ft-lbs on the barrel. I will go a little less than 90 with the bare metal but never closer than 60. Regardless of whether you use the washers, shims, or decide to file it, get it to where you can hand fit it to around 90 degrees short of where you want it, then torque it on. The only drawbacks to that process are removing the finish off the back end of the device, and the possibility of getting it out of square. After being instructed by Dale of Elite Iron to do that with his compensator suppressor mounts, I now use that process for all muzzle devices. I have gotten to the point of not even using crush or peel washers, anymore, but instead I file down the back end of it on my belt/disk sander using guides to keep it square until it lines up.
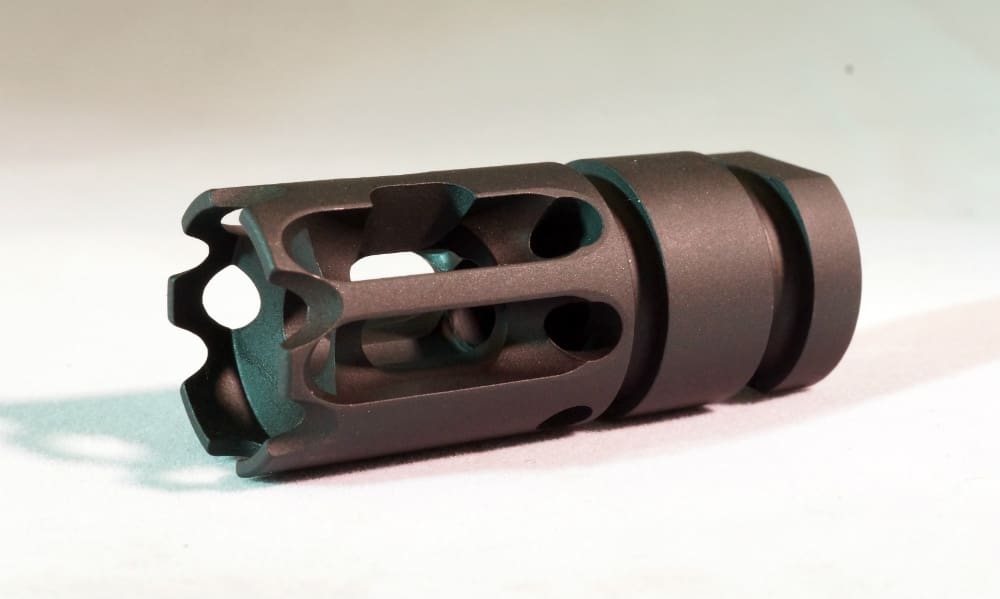
I prefer a simple open end wrench on muzzle devices. It's now solely for castle and barrel nuts. I have an armourer's tool, but I have only ever used that on one single muzzle device. The best way to orient (commonly referred to as "timing") a muzzle device isn't as dependent upon tools, as it is on the process. The best tool is the one between your ears. If you are not a stickler for accuracy and don't care about a precise crown, then disregard this periodic cleaning. Left uncleaned, this fouling will definitely corrode the surface of the crown. The idea is to make it easy to remove the MD from time to time in order to clean the fouling off the muzzle crown. Sand the bottom of the crush washer sufficiently so the MD can be screwed to the right orientation without crushing the washer too much. Otherwise, the MD could become very difficult to remove.ģ.
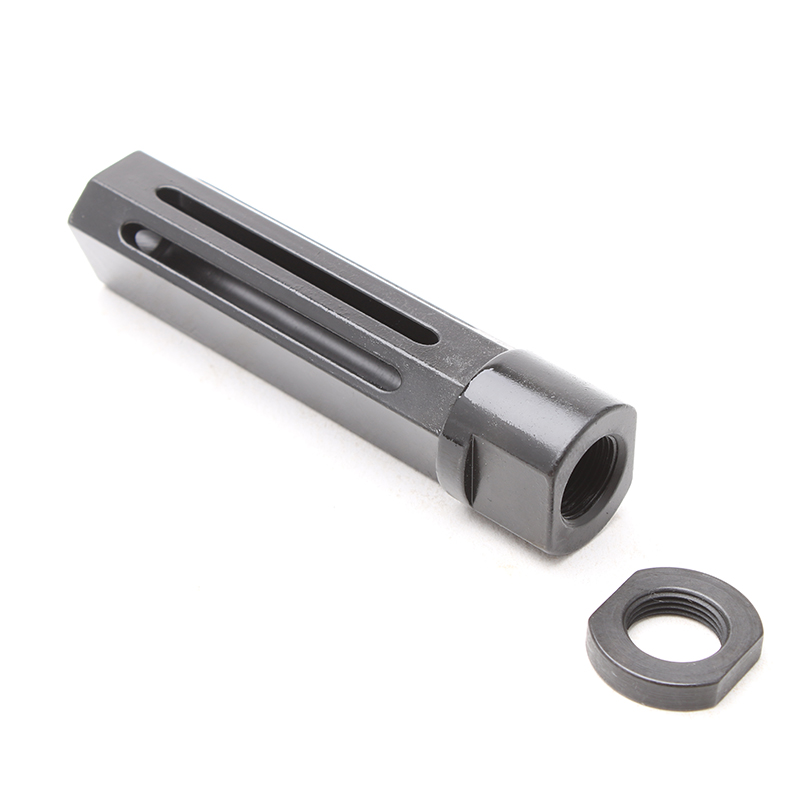
Apply moly grease to the threads and to both sides of the crush washer, if used. The hole between the two blocks is drilled one size smaller than the diameter of the barrel where clamped (e.g., 11/16" drill for a. My blocks were made from a piece of pine 2x4, with the grain perpendicular to the bore axis. This prevents torque from being translated to the barrel/receiver interface. Clamp the exposed portion of the barrel with a pair of wood blocks in a sturdy bench vise. My method for installing and timing muzzle devices involves the following steps:ġ.
